YU Shuhong and WU Hengan co-reported a new bioinspired super-elastic and fatigue resistant carbon materials. This work is published in Nature Communications entitled “
Super-elastic and fatigue resistant carbon material with lamellar multi-arch microstructure”.
Low-density compressible materials with high compressibility, superior elasticity and fatigue resistance are of great significance due to their promising application potential.However, high compressibility, superior elasticity and fatigue resistance are generally mutually exclusive and hardly to be optimized simultaneously because microstructure cracking or buckling failure of these materials is inevitable when they undergo large strain cyclic compression processes. These microstructural damages then lead to inferior elasticity with slow recovery speed and large energy dissipation, as well as permanent fatigue failure of these materials.
Inspired by the conceptual basis of some macro-arches from daily life, typically the arches of human foot (act as elastic spring-type cushioning system to facilitate human motions), YU et al. addressed this microstructural problem by designing a macroscopic carbon material with numerous micro-arches aligned along preferred direction in a stagger stacking manner to serve as its elastic origin. Via designing such lamellar micro-arch structure, the obtained monolithic material, though is composed of brittle amorphous carbon-graphene (C-G) composite constituent, achieves a combination of high compressibility, superior elasticity and fatigue resistance simultaneously. It can completely recover to its original shape upon 90% compression strain with small energy dissipation of ~0.2 (obviously lower than that of all previously reported value of 0.3-0.7) and can rebound a steel ball in spring-like fashion with fast recovery speed of ~580 mm/s (more than three times of previously reported maximum value of 170 mm/s). Moreover, it can undergo more than 1.0×106 compression cycles at 20% strain, 2.5×105 cycles at 50% strain and 1.0×104 cycles at 80% strain yet still sustains its structural integrity, which is even superior than that of the state-of-the-art structural materials composed of strong and robust solid constituents.
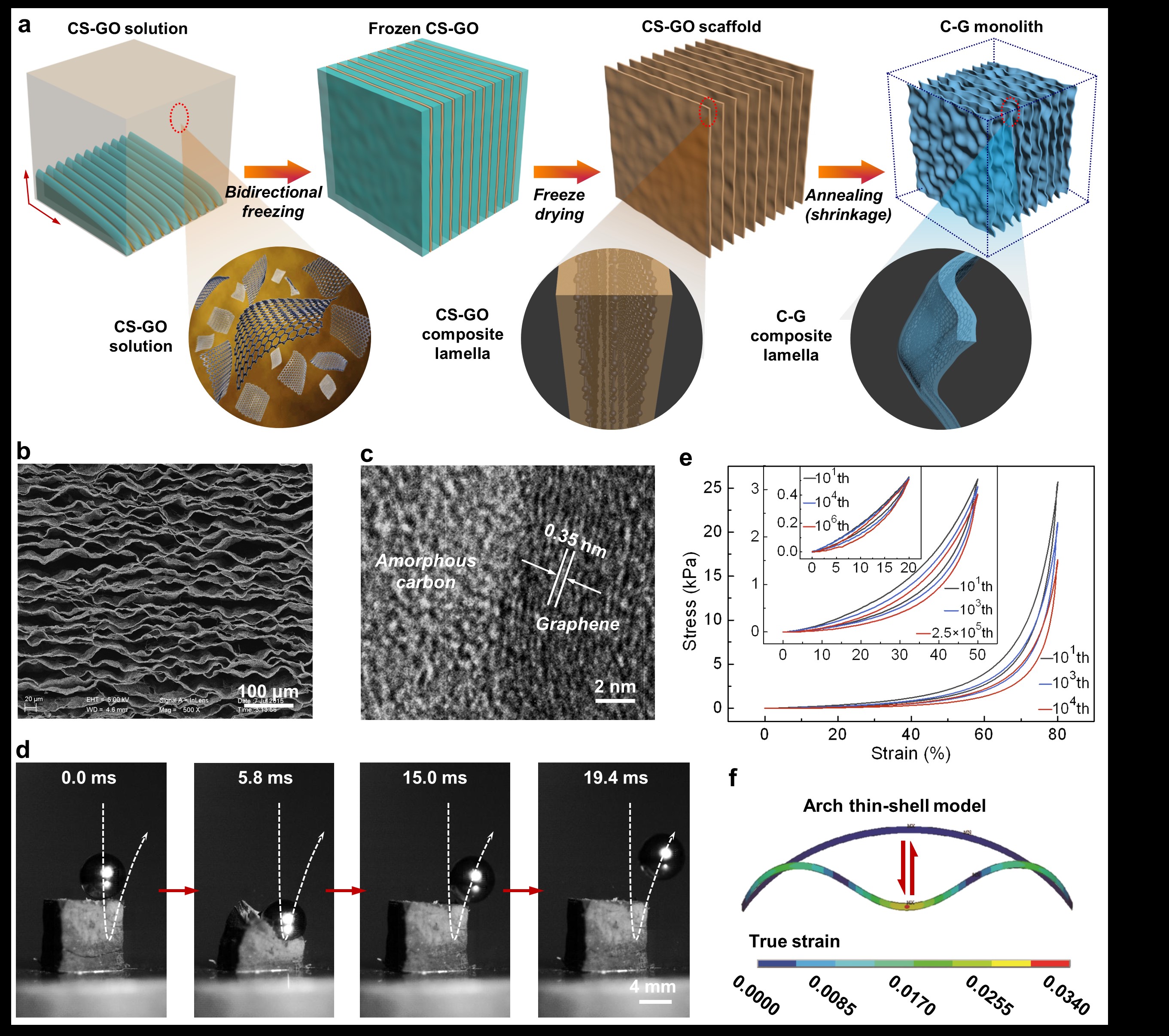
Figure. Elastic carbon monolith based on micro-arch structural design. (a) Schematic illustration showing the fabrication process of the carbon elastomer. (b) SEM image showing the lamellar multi-arch microstructure of the carbon elastomer. (c) High resolution TEM image showing that the lamella is composed of amorphous carbon and graphene composite. (d) Real-time images from high-speed camera showing that the carbonelastomer can rebound a steel ball at large speed, in a spring-like fashion. (e) Stress–strain curves of the carbon elastomers at 20% strain for 1×106 cycles, at 50% strain for 2.5×105 cycles and at 80% strain for 1×104 cycles. (f)The true material strain (von Mises total strain) profiles of the cylindrical shell model under large geometry deformation.
According to Professor YU, in order to achieve this hierarchical structure, they firstly developed a bidirectional freezing method to fabricate a monolithic chitosan-graphene oxide (CS-GO) composite scaffold consists of numerous parallel, aligned and thin lamellas. Then, the scaffold was treated with annealing to crumple each flat lamellas into waved micro-arch morphology on the base of different degree of local volume decrease of the CS matrix and the embedded GO sheets in this carbonization process. The ingenious combination of the two step ensures that all the micro-arches in the carbon monolith have the same direction, which can play the elastic role simultaneously when the carbon monolith undergoing compression process.
The superior performance of this material was then systematically investigated by using mechanical simulations conducted by WU et al., which reveal that the thin-shell micro-arches display typical elastic behavior, and can undergo large out-of-plane deformation without yielding because of the small in-plane material strain. These intrinsic features of the micro-arch structural unit determine the unique performances of the final monolithic materials.
The carbon material exhibits the application potential for mechanical sensors (such as detection of seismic waves) in some extreme environment due to its intrinsic properties. This successful case of replicating mechanical performance of macro-arches into micro-arches will provide guidelines for developing bran-new microstructural materials.
This work is acknowledged by the funding support from the Foundation for Innovative Research Groups of the National Natural Science Foundation of China, the National Natural Science Foundation of China, the National Basic Research Program of China, the Users with Excellence and Scientific Research Grant of Hefei Science Center of CAS, and the Chinese Academy of Sciences.
Paper Link:http://www.nature.com/ncomms/2016/160927/ncomms12920/full/ncomms12920.html
(Hefei National Laboratory for Physical Sciences at the Microscale, Division of Nanomaterials & Chemistry, Collaborative Innovation Center of Suzh ou Nano Science and Technology, Hefei Science Center, Research Department, USTC News Center)