3D printing, also known as additive manufacturing, offers resolution to fabricate various physical objects. However, one of the critical issues of 3D printing is that the sizes of fabricated objects are limited by the 3D printer’s working volume. Therefore, it is worth developing a computational solution to fabricate large objects and satisfy various fabrication requirements.
Recently, a fast and cost-effective technique for fabricating large 3D objects was developed by Prof. LIU Ligang and Prof. SONG Peng at the University of Science & Technology of China (USTC). This study has been accepted by the 43rd International Conference on Computer Graphics and Interactive Techniques (SIGGRAPH 2016).
The research attempted to represent a given 3D shape as multiple coarse polyhedral bases inside the object and a fine geometric shell over the bases by taking advantage of the complementary strengths of 2D laser cutting. This method can provide a rapid and low-cost solution for 2D manufacturing and 3D printing to achieve the research design requirements.
Considering the components’ aesthetics, stability and balancing in this work, the bases, which produced by laser cutters with low material cost and high fabrication speed, are assembled with a well-designed network of interlocking joints. The shell, which can be further decomposed into thin pieces, is realized by 3D printers and attached to the bases with printed screws and bolts.
The results show that it can save 60% of the total material and time cost comparing to a simple partitioning method. This research has drawn great attention from the 3D printing industry and some people have expressed their intention to collaborate on commercializing the techniques.
This work is supported by the National Natural Science Fund for Excellent Young Scholars of China, the Young Scientists Fund of the National Natural Science Foundation of China, and the One Hundred Talent Project of the Chinese Academy of Sciences.
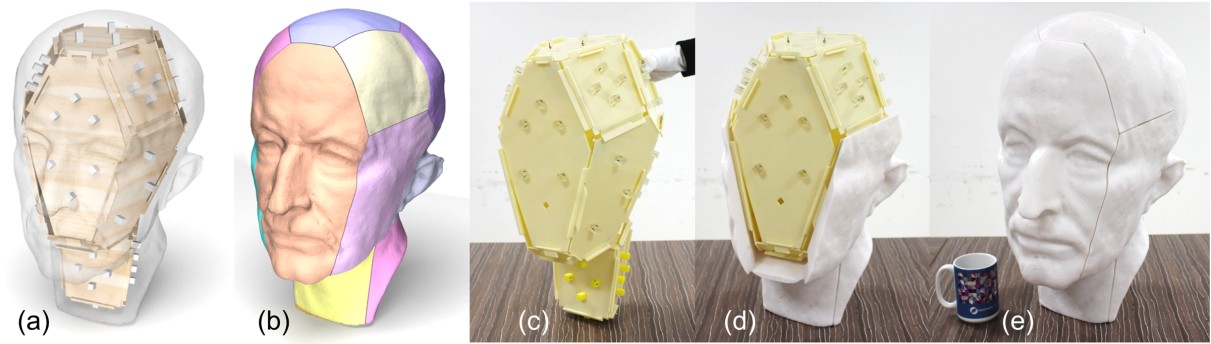
Figure 1. A computational solution to fabricate large objects is developed by taking advantage of the complementary strengths of 3D printing and 2D laser cutting.
The Maker Space is located in the 12nd Floor of Management and Research Building, School of Mathematical Sciences, East Campus, USTC. Various kinds of facilities include 3D printers, laser-cutting machine, 6-axis robot arm, mobile robot platform, unmanned aerial vehicle and toolkits offer an open environment and experimental platform for undergraduate students to create innovative hardware and software. A number of research papers from the members of Maker Space have been published on distinguished international journals. WANG Ziqi, a junior student from the School of Mathematical Sciences and also an intern in the Maker Space, is one of the major contributors of this research project.

Figure 2. The Maker Space in the School of Mathematical Sciences
The first author, Assoc. Prof. Peng Song, is from the School of Computer Sciences and Technology, and the corresponding author, Prof. Ligang Liu, is from the School of Mathematical Sciences.
This work is supported by the National Natural Science Fund for Excellent Young Scholars of China, the Young Scientists Fund of the National Natural Science Foundation of China, and the One Hundred Talent Project of the Chinese Academy of Sciences.
(TANG Lijia, School of Mathematical Sciences)